Getting hold of materials that you can trust to be right can sometimes represent something of a problem. It might be that you need to have panels made from a particular material or you are making a triptych and you need to have metal hinges that are made from the same materials that were available 600 years ago
Other pages will tell you about making things but this page is about obtaining the materials in the first place. Here, we'll cover:
- Charcoal Iron;
- Quarter Sawn Oak; and,
- Gold and Other Metal Leaf.
Charcoal Iron
A bit about the history and why it is difficult to get
When I did metalwork at school, one of the teachers made some wrought iron gates for someone he knew, building them from mild steel bar stock. Online, you can buy wrought iron nails, hinges and all manner of things.
Except that it is not wrought iron.
Wrought iron is a material, not a type of construction.
- Originally, iron was made by mixing charcoal with iron ore and heating it up. The carbon in the charcoal would grab the
oxygen from the iron ore, exiting as a gas and leaving the reduced iron metal behind as a bloom. In addition, the iron ore contains
silica and of course, when the iron forms, it includes chunks of charcoal. The iron never melts in the furnace - if it was allowed
to, the liquid iron would absorb carbon from the charcoal to produce a high carbon pig iron which was not desirable.
When the iron is taken out of the furnace, it is hammered which, apart from making it form a useful iron lump,
makes the larger charcoal lumps fall out. However, it tends to break up the remaining charcoal, leaving smaller bits behind.
Another thing that is in the final iron is the silica from the impurities in the iron ore. This forms sort of glass fibres
that run throughout the iron, making it a composite which turns out to be very strong, malleable and resistant to corrosion.
- The process was then modified so that iron was melted in the furnace and cast to form pig iron which was high in carbon.
Being an alloy - yes, iron and carbon are considered an alloy - it has a lower melting point so it was put into what was
called a puddle furnace where a puddle of molten pig iron was exposed to the air which preferentially oxidised the carbon,
reducing the proportion in the iron and making it solidify. This was then removed and then hammered to form it as before
with the charcoal iron.
This new iron still had the silicates in it making it a composite as before and as before, it was strong
malleable and resistant to corrosion. The difference was that it didn't have the inclusions of charcoal in it.
- The process was modified again, this time, instead of the puddle furnace, you melt your pig iron in a large pot and then
pump oxygen through it to remove the carbon - the Bessemer converter.
Wrought iron was so good a material that there was even a way of converting the steel from a Bessemer converter to a
type of wrought iron developed by James Aston in the USA where iron from the converter was poured into slightly cooler slag
where it mixed and was then worked and rolled so that it had a similar structure to wrought iron.
Nowadays, virtually all so-called wrought iron things are made from mild steel and just given a superficial 'hammered' look so
they are not actually wrought iron.
So, why do we need charcoal iron? Simply, around the time of the renaissance, 600 years ago, iron production hadn't got past the
charcoal process so if a fitting that is needed is going to look the part, it needs to be made out of the correct material. Brass didn't
exist so it had to be charcoal iron.
Getting hold of it
This planet still has one supplier of wrought iron and it is The Real Wrought Iron Company, based at Topp & Co., Tholthorpe, North Yorkshire (UK). They travel around sourcing genuine wrought iron and making sheet, plate and various sections for railings, handrails and so on.
Included is charcoal iron as sheet which is ideal for the my needs. I have several samples of this stuff and it certainly is
different to the stuff passing itself off on the internet as 'wrought iron'. The sizes are all imperial so 3/32" is roughly 2.4mm and 1/16" is roughly 1.6mm.
Quarter Sawn Oak
A bit about the history and why it is difficult to get
Quarter sawn oak panel was the material of choice, six hundred years ago, as it produced a surface that was flat enough to paint details on that
could be as fine as 100-200 microns - ideal for fine details on faces, buildings and so on, often painting individual hairs.
This material had several advantages:
being quarter sawn, the grain runs across the panel as you can see from the image on the right. When wood absorbs water from the atmosphere,
the harder and softer parts of the grain absorb it differently and expand differently. If the grain runs parallel to the surface or at an
angle, the wooden panel will spoon, twist and otherwise warp which is wholly undesirable for a painting. However, if the wood has the grain
running across it, it will not warp.
This was known about in the 15th century and this is what the Flemish paintings were painted on at the beginning of the renaissance around 1400. However, much later,
when the Italians started to have their renaissance, after Jan van Eyck had died, it was as though that had been forgotten about and they used
planks that had been cut across the trunk so the grain travelled through the panel in great arcs and when it changed its moisture content, it
warped terribly.
In fact, the warping was so bad that in parts of the panel where the rings curved the most, they would cut that bit out and replace it with
a piece of wood that had a flatter ring structure in it.
The reason it is difficult to get seems to be that virtually all wood is cut simply in planks that go across the wood without regard to the
direction of the rings. To cut planks where the grain runs across the plank as in these pictures here, you need to cut the wood radially. Originally, it was produced by splitting the trunk radially so that you would end up with a set of wedge-shaped planks and if you look at the old Flemish paintings, that is exactly what they are painted on.
Getting hold of it
The fact that virtually all planks are just cut
across the trunk regardless of grain makes it easy and cost effective for the saw mills. However, if you want a piece of wood that is
going to last and not warp, you want the real thing.
Split radial oak is really something that if nothing else will do, you are going to have to do it yourself.
When I was searching for a supplier, I kept on encountering companies that would sell you anything as long as it was waxed or oiled
so that it would be all right if you wanted to use it for a floor. Getting hold of untreated, radially (quarter sawn) oak was a real problem.
Quarter Sawn Oak, however is available online and you can order as much or little as you like. These people don't do anything else and
they know what they are doing. I get my panels from them, they are The Quarter Sawn Oak
Company, based in Edale, Derbyshire (UK) and sell to DIY and trade.
This is a piece of untreated, planed all around, quarter-sawn oak panel that is roughly 10" x 12"
(25 x 30cm) and 9mm thick bought directly from them. In my experience, the company is helpful, delivers on time, is not expensive
and the wood they supply is excellent quality and the correct size.
This is a nice size to work with for doing portraits. As untreated, it is already smoother than canvas; when it is treated,
it is smooth to the level of a shine and you can put in an incredible level of detail with it.
Gold and Other Metal Leaf / Powder
A bit about the history and why it is difficult to get
Leaf
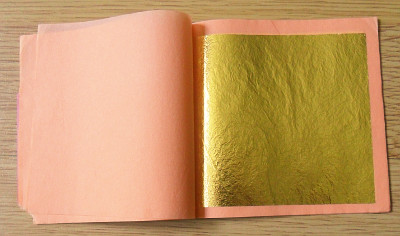
Gold is extremely malleable - it can be beaten into shapes very easily - and can therefore be beaten into the very thin flat sheets
that we call gold leaf. Modern gold leaf is thin enough to be slightly transparent - reflecting infrared, red and yellow light, the
light that is transmitted appears as a greenish blue. The thickness of ancient gold leaf was around 10 times thicker than modern gold
leaf and by the time of the middle ages, it was around five times. It should also be noted that in the middle ages, there were
sufficient impurities in the smelting process for gold to be a little on the orange side so, without a name for orange (foxes and robins
were described as red even though they are an orange colour), gold was sometimes described as 'red' coloured
Other metals can also be beaten into thin leaf: silver, tin, copper and more recently, palladium, platinum and aluminium - the latter
being used as a cheap alternative to silver leaf. A type of brass called Dutch metal, gilt or Schlag metal is also beaten into thin sheets
and used as a cheap alternative to gold leaf.
Gold can be supplied in various alloys with other metals such as copper, silver, nickel and this is where you get:
- 'rose gold' - with copper;
- 'white gold' - with a white metal usually silver but can be palladium or nickel;
- 'green gold' - a naturally occurring alloy of silver and gold;
- and so on.
Equally, with imitation gold, you can get schlag metal with differing amounts of zinc and copper to imitate the gold alloys.
These are:
ID | Name | Percentage Copper | Percentage Zinc | Imitating... |
No 1 | Red Gold | 90 | 10 | 18ct red |
No 2 | Orange or Warm Gold | 88 | 12 | 22ct |
No 2.1 | intermediate shade |
No 2.2 | intermediate shade |
No 2.5 | Standard Gold | 85 | 15 | 23.5ct |
No 3 | Yellow Gold | 82 | 18 | 18ct yellow |
There are pros and cons to using imitation gold leaf:
Cost |
Pro |
A box of 1,000 160x160mm leaves of Schlag costs about the same as a book of 25 leaves of 80x80mm 24ct gold. This is the difference
between covering 0.16m2 and covering 25.6m2. |
|
Thickness |
Pro |
Schlag is quite a bit thicker than gold so it doesn't tear and can put up with rougher handling than gold leaf. |
Con |
The extra strength means that it can pull away from the surface when you are cleaning up loose leaf. |
|
Reactivity |
Pro |
Schlaf will react so you can paint a solution of sodium or potassium sulphide on it to create a layer of metal sulphide that has a thickness that is
in the order of the wavelength of light, thus producing interference colours of straw/yellow, magenta, cyan and so on, that you can use artistically. |
Con |
Gold is a noble metal whereas copper and zinc are not - they will oxidise over time so you need to paint a varnish or
other protective layer over the top to stop tarnishing. |
I wondered just how much gold there was in normal thickness modern gold leaf so I weight the book before and after using two sheets of it and
on a two figure balance, it lost 30mg. So, with a fair amount of latitude for error, that is around 15mg per sheet. This makes the thickness around
12 microns and for those who think that gold leaf is transparent because it is only about 7 atoms thick, that works out to be around 800 million
atoms thick.
Powder
Both gold and silver and various alloys can be obtained as finely divided powders that can then be added to acacia gum in water to
make what is known as - for historical reasons - 'shell gold/silver.' This is because it was stored in sea shells - the modern
equivalent being a half or quarter pan watercolour container.
You use it like a watercolour so you paint it on very thinly and when it is dry, you can either leave it as a sparkling semi-matt finish or you can rub the surface with a hard, smooth stone - usually agate - so that the surface of acacia gum is rubbed off leaving the gold which is so malleable that the force from the burnishing stone spreads it over the adjacent gold and fuses it together into a single, flat surface that reflects light as a mirror would.
You can have some gold left untouched and some burnished so as to produce a desirable effect should you so wish. You can purchase burnishing tools in a wide variety of shapes and sizes to achieve just what you want.
Getting hold of it
Getting hold of gold leaf might not seem that hard to start with - it is advertised all over the place - but you need to take care
when assessing a source because there are a number of things that can go wrong:
- The gold might not be as pure as it says - some advertisers think that 'pure gold' is around 90%;
- The sheets might be a size that is more expensive than it seems; and,
- It might be delivered in a way such that the gold leaf you end up with could be broken up in transit.
When I first started out on this, I tried all of the cheaper options such as buying 24kt gold leaf from other online sellers with
varying results. One of them had so much copper in it that it turned green on the painting. You might need only a small amount of gold
leaf for a particular job but buying 45mm squares of it isn't necessarily the best thing that you can do.
Gold leaf normally comes in 80mm square sheets which is supposed to be the width of a man's hand although it is so fragile that you
would never pick it up like that. At that size, it is priced in the year 2020 at around GBP1.00 per sheet including VAT. You can, if
you only need that much or are experimenting, obtain it in books of five sheets but normally it is sold in books of 25 sheets.
This is a 25 sheet book from a trusted supplier. It cost around GBP25 once shipping and VAT had been added but I know that it can be trusted.
For a given area, it worked out to be about the same as the 45mm square sheets from the other supplier except that this didn't go green.
In case you are wondering why the corners of a number of sheets are torn off, it makes it easier to find the next page of leaf if you do
that once you have used the leaf from that page.
Remembering that medieval gold leaf was around five the thickness that it is today and in ancient times, it was around ten times
the thickness, it is possible to buy gold leaf that is thicker than standard gold leaf and it is noticeably more opaque without
costing a great deal more.
Other gold alloys are cheaper than 24ct but I only use 24 carat because you know that the level of other metals is almost non-existent
if you are trying to match it on your own work for repairs and so on. If you are repairing somebody else's gold leaf work, you would probably be better off with one of your supplier's sample books so that you can pick the correct colour.
Lastly, remember that an artifact of using gold that is less than 24 carat is that the metals that it is alloyed with will react
with their environment so if copper is added to the gold, it will go green when it reacts with the carbon dioxide in the air. If
silver is added to the gold remember that will react with sulphides in the air, and so on. In these cases, the gold will need
protecting with a layer of varnish of some sort as does schlag metal, silver, copper and so on.
The suppliers that I use in the UK are: Gold Leaf Supplies; and, Wrights of Lymm. A supplier of other gold/metal leaf related things include also, Handover.
All images and original artwork Copyright ©2017-2020 Paul Alan Grosse.